Warehouse Management knowledge base
Expert insights into the world of the WMS
Over the past 22 years we've helped a growing number of businesses achieve success in their warehouses. Find out how and see the results in our collection of case studies.
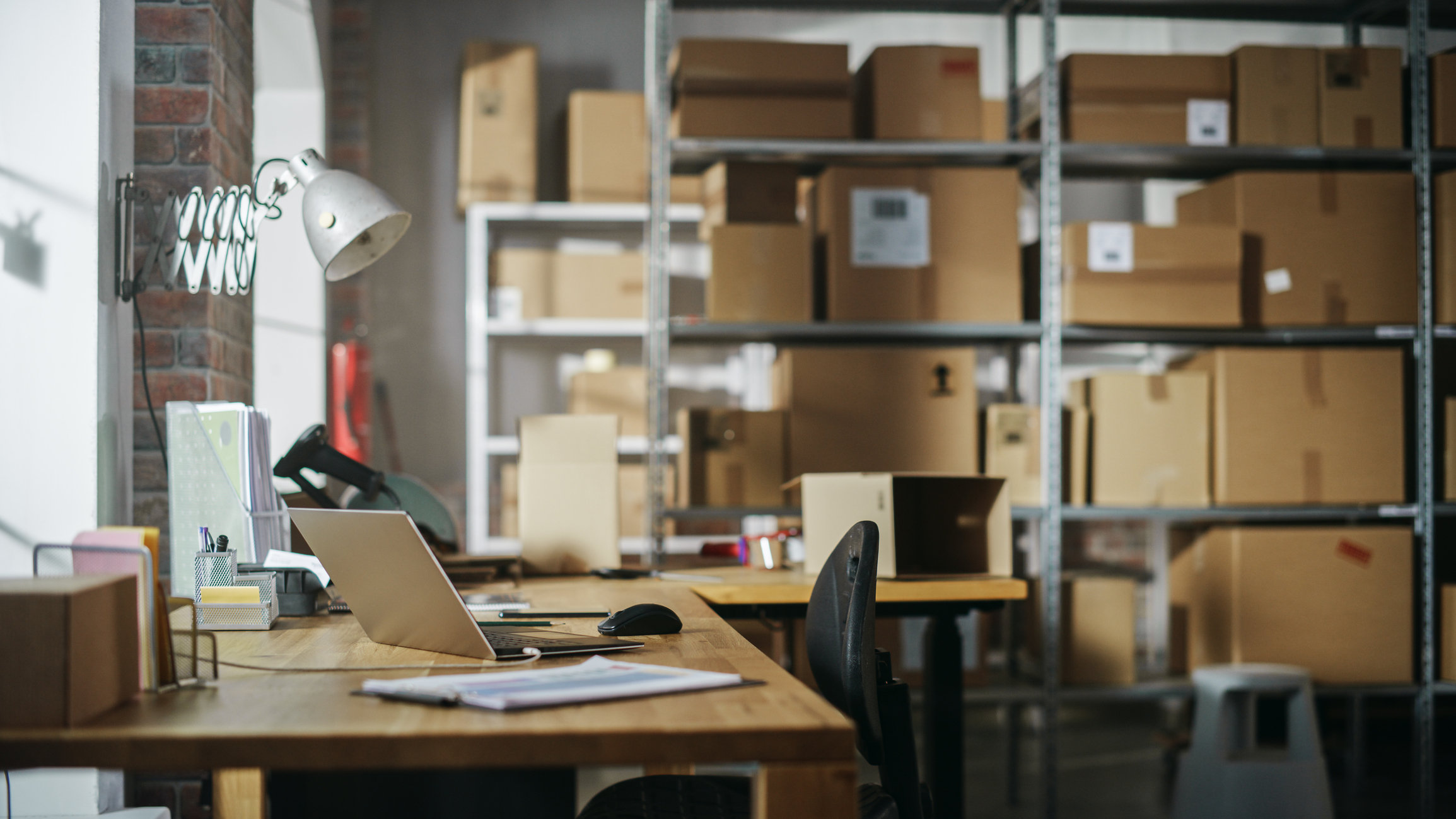
The Advantages of a Warehouse Management System for a Small Business
A WMS helps small businesses boost efficiency, accuracy, and stay competitive.
Continue reading...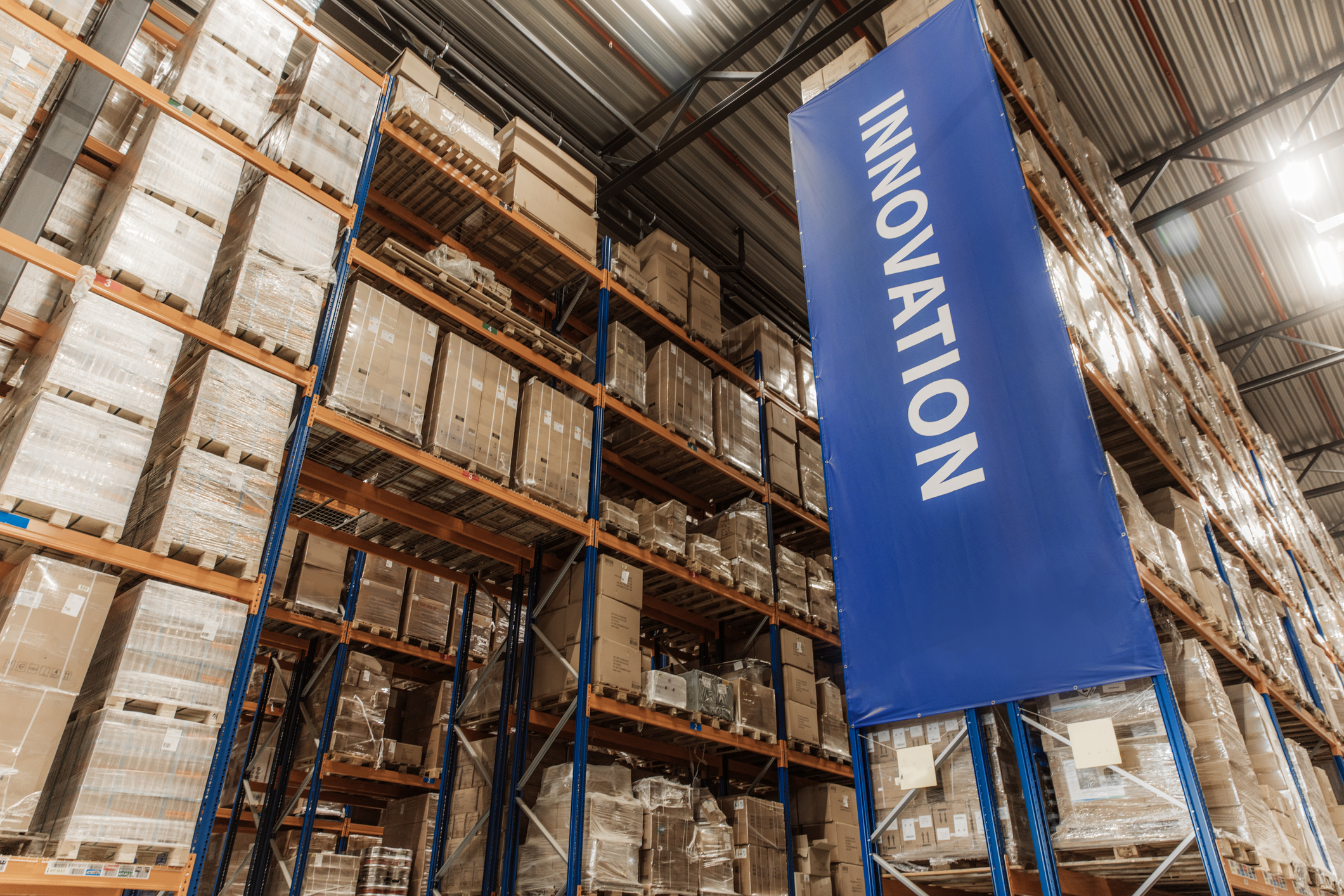
The Future of Warehouse Management: Key Trends for 2025
Top WMS trends for 2025 to boost efficiency, cut waste & future-proof your warehouse
Continue reading...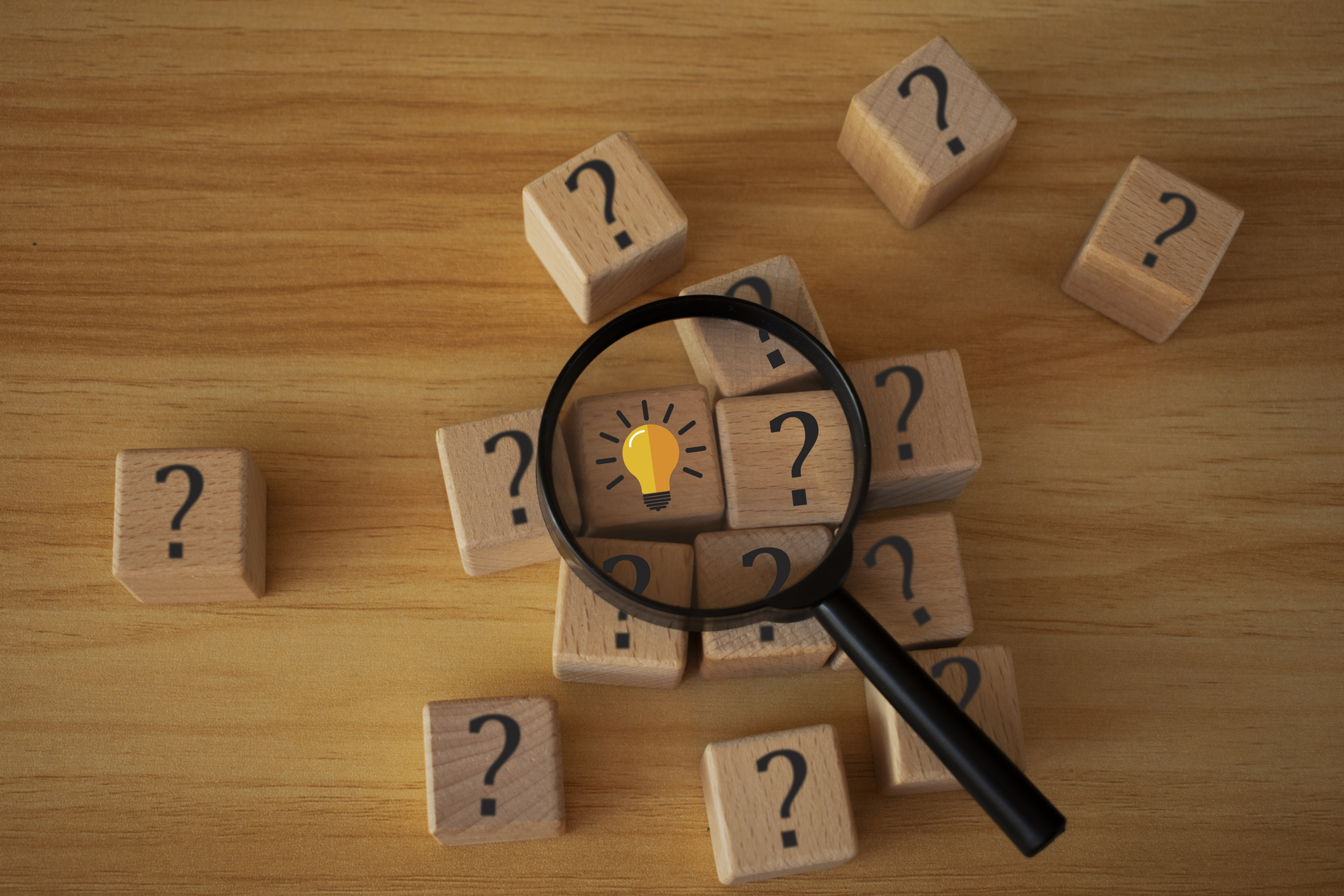
Struggling to find a WMS that solves a problem?
Most WMS handle the basics, but unique operations often need more than standard solutions.
Continue reading...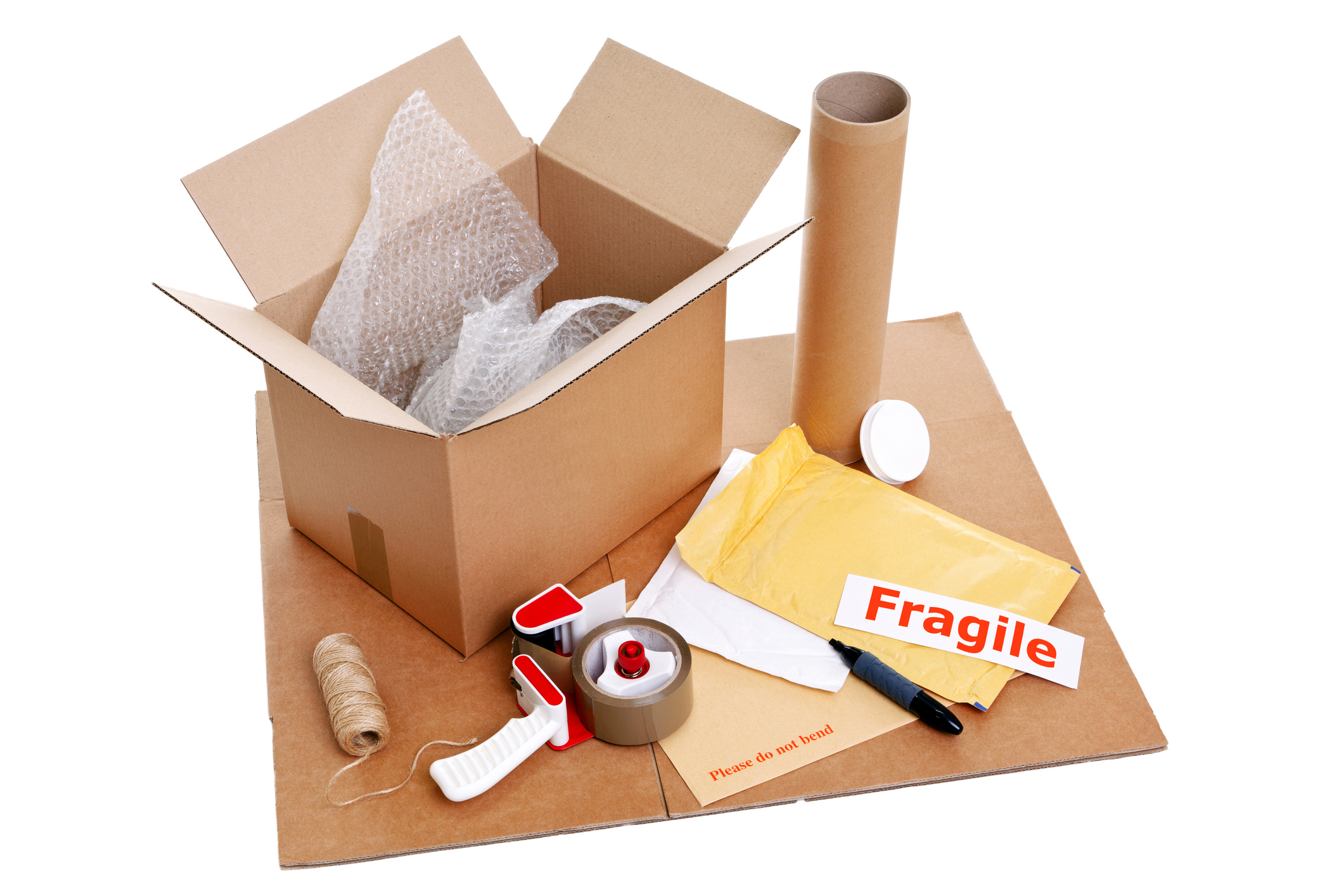
Introducing Optima WMS Consumables Module - Don't Overlook Your Warehouse's Unsung Hero
Warehouse consumables impact costs, efficiency, and customer satisfaction more than you think.
Continue reading...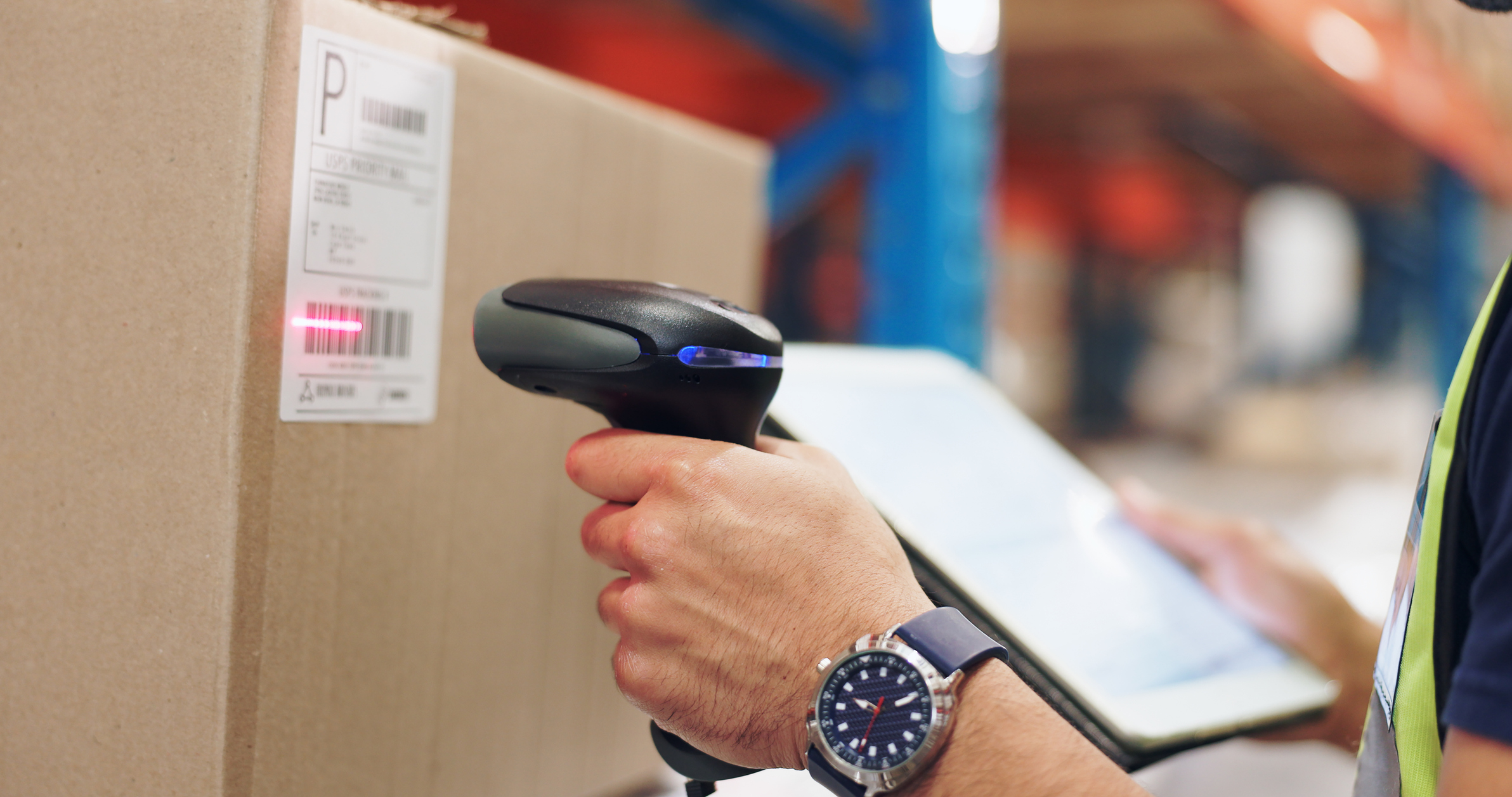
Introducing the Optima WMS Tasks Module – A Revolution in Warehouse Agility
Optima rebuilt its WMS from scratch to deliver unmatched agility in warehouse operations.
Continue reading...Optima Fully Integrated with Shopify
Optima WMS integrates seamlessly to boost efficiency and reduce manual processes.
Continue reading...Optima Fully Integrated with DPD Ship@Ease
Optima WMS uses seamless integrations to improve efficiency and cut manual processes.
Continue reading...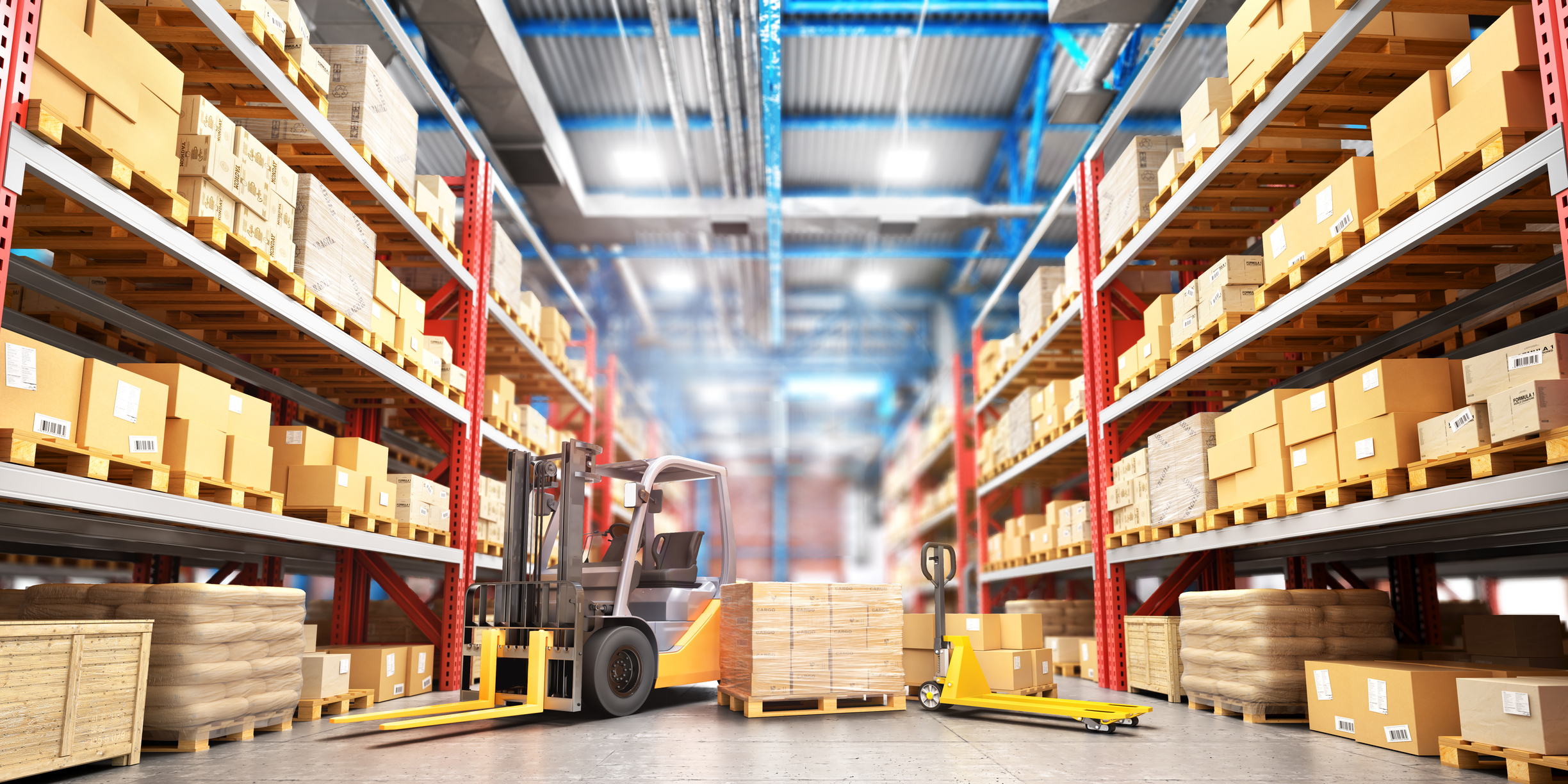
Top 5 Benefits Of Automated Warehouse Solutions For Your Business
Automate your warehouse to cut costs, boost accuracy, and scale efficiently with the right WMS.
Continue reading...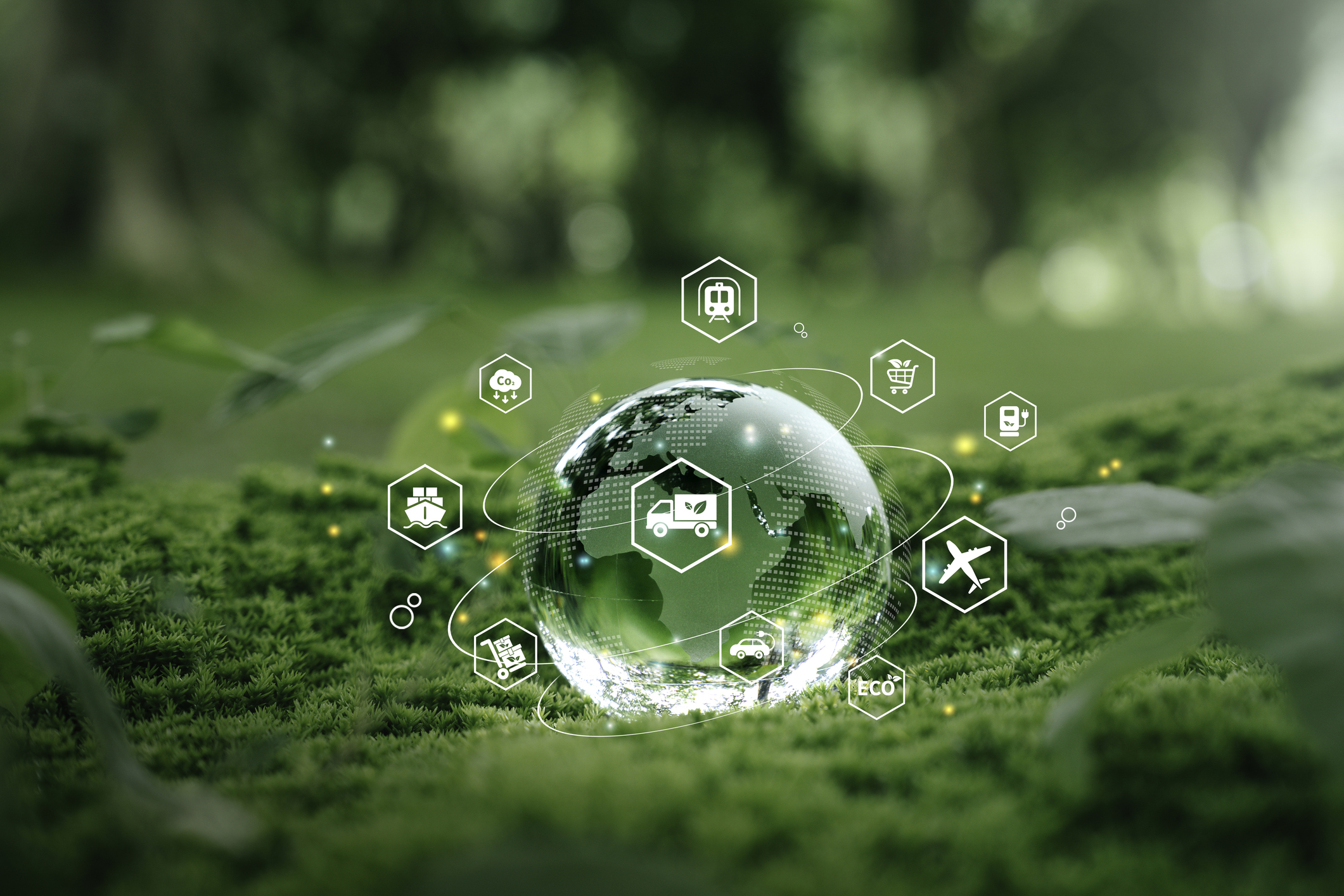
Sustainable Warehousing: Future-proofing Your Supply Chain with Optima WMS
In today's world, sustainability is no longer a choice - it's a necessity. As environmental concerns grow and regulatory pressures increase, businesses must look for innovative ways to reduce their carbon footprint while maintaining operational efficiency. Warehousing, a critical component of the supply chain, presents significant opportunities for sustainable improvements.
Continue reading...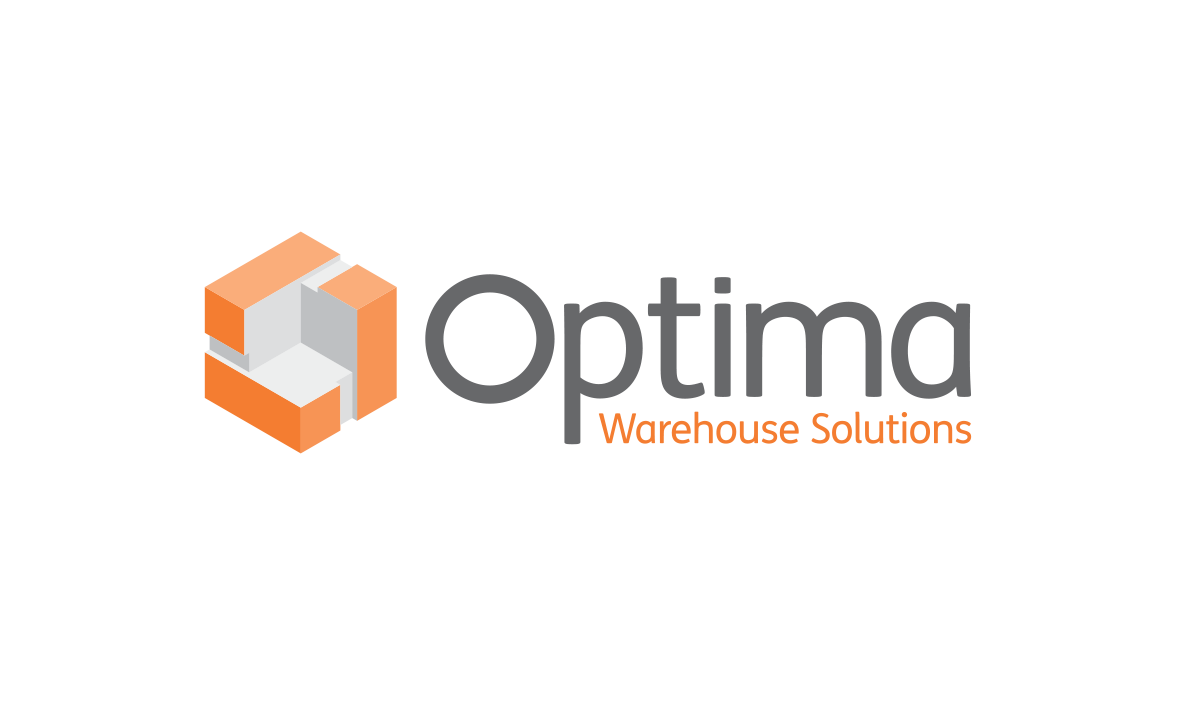
Does My Business Need a WMS?
A Warehouse Management System (WMS) is a way to streamline business, maximise profit, and increase customer satisfaction, but, does your brand need a WMS? Let’s break it down.
Continue reading...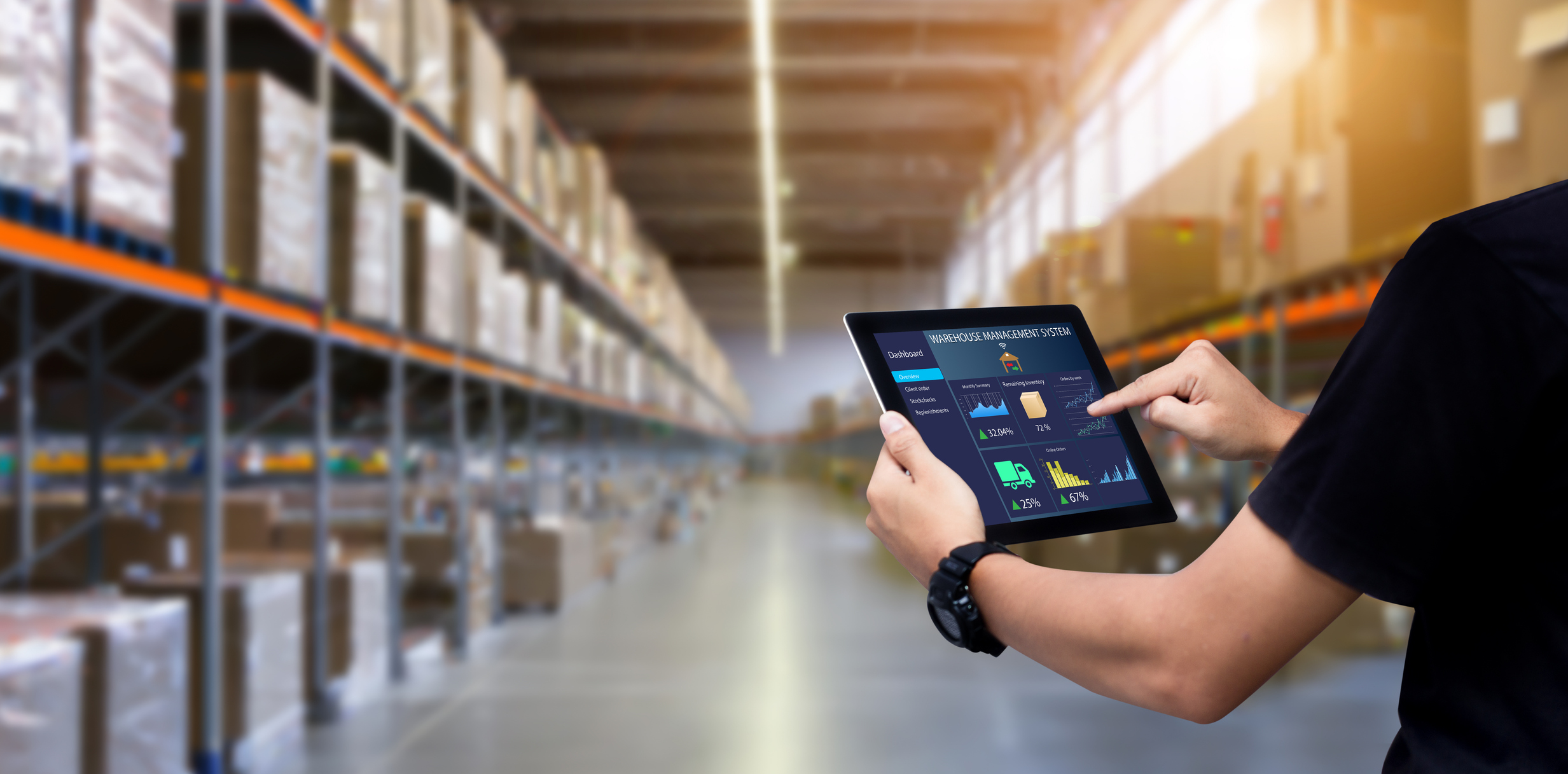
Managing Stock Levels
Any business involved in the supply of goods must have an effective stock management system in place, as managing inventory is no simple task. Seasonal fluctuations, economic conditions, space limitations, delivery timelines, and customer demands all play a role in stock management challenges.
Continue reading...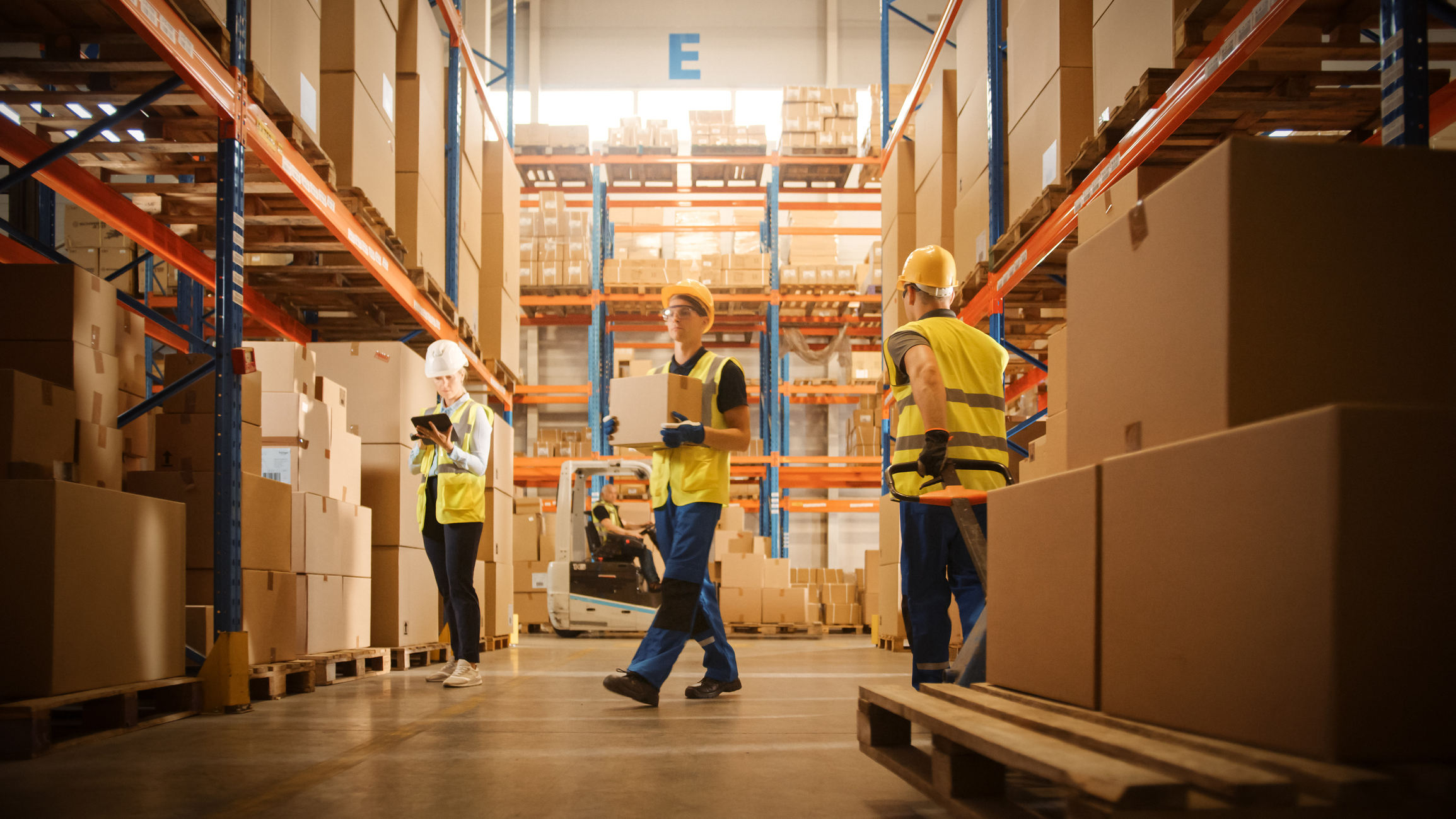
The Many Roles in a Warehouse: How a WMS Enhances Efficiency
A Warehouse Management System (WMS) is the key to optimising workflows, improving accuracy, and ensuring seamless operations. Let's explore five essential warehouse roles and how a WMS can enhance their productivity.
Continue reading...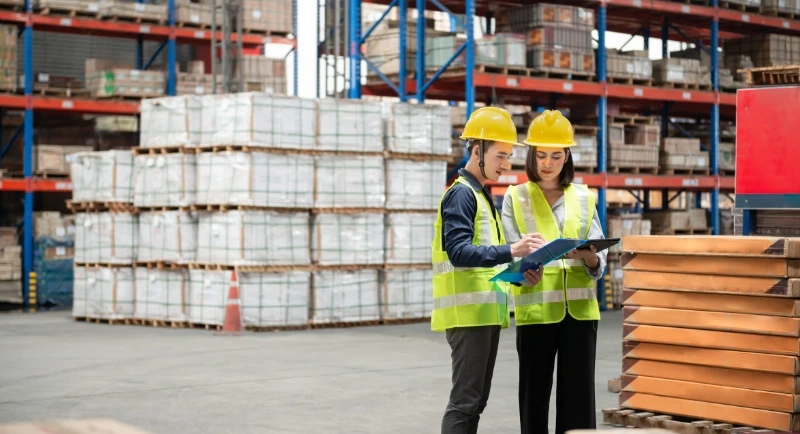
Types of Warehouses for ecommerce.
When setting up your eCommerce business, one question you may ask is, where will I store my goods until they are sold online? There are many types of warehouses that allow you to store the goods that are being sold online, record sales and accurately track the inventory to prevent lost items. Warehousing is a great option for growing online businesses that have outgrown their current storage facility. There are many types of warehouses for eCommerce businesses to consider such as public, private, bonded, consolidated and smart warehouses.
Continue reading...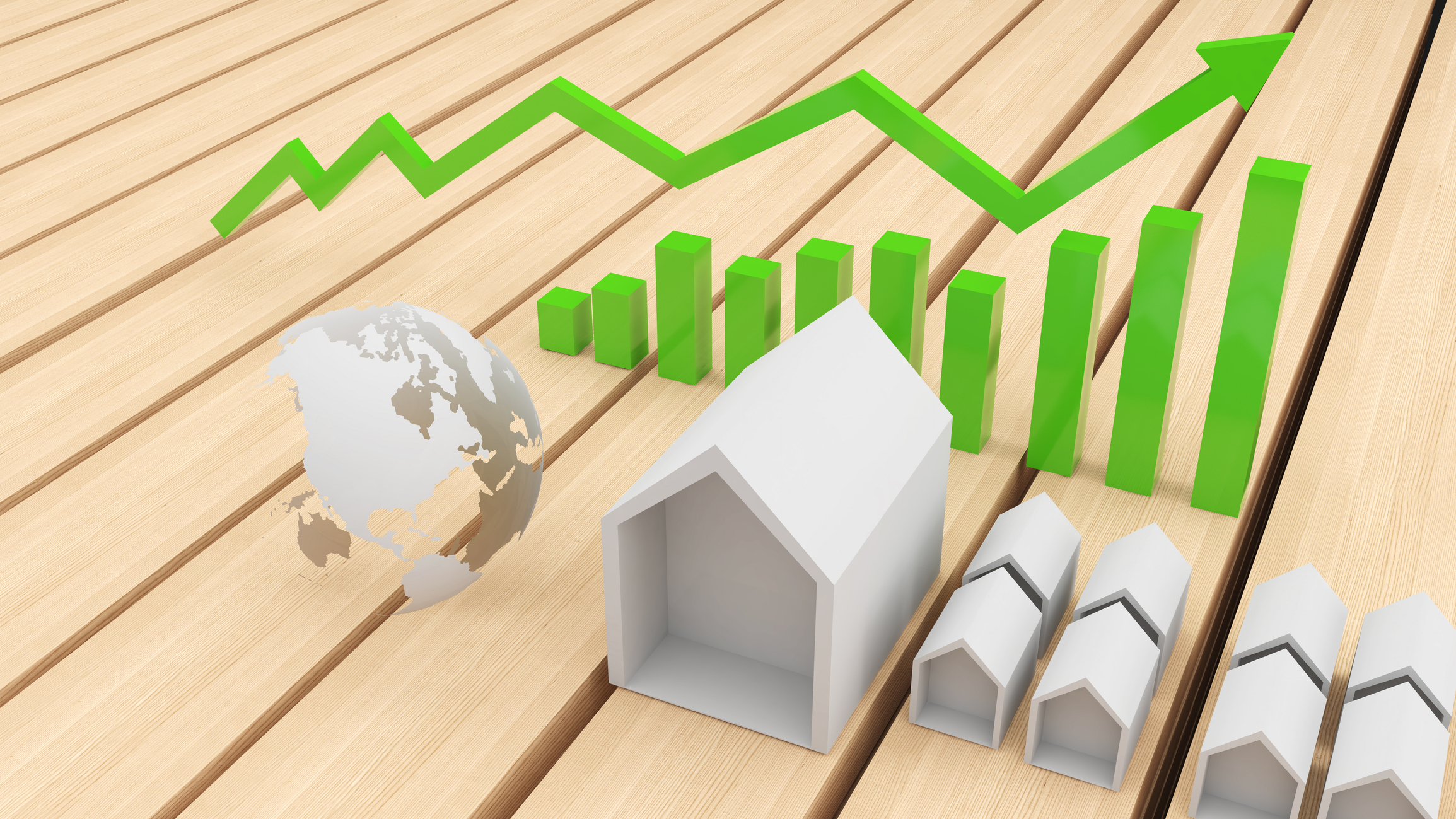
Top 5 Warehouse Challenges For Growing Businesses
Every business starts with a vision, but as it grows, new challenges emerge that can make or break its success. While growth is an exciting phase, it also brings complexities that require strategic planning and adaptability.
Continue reading...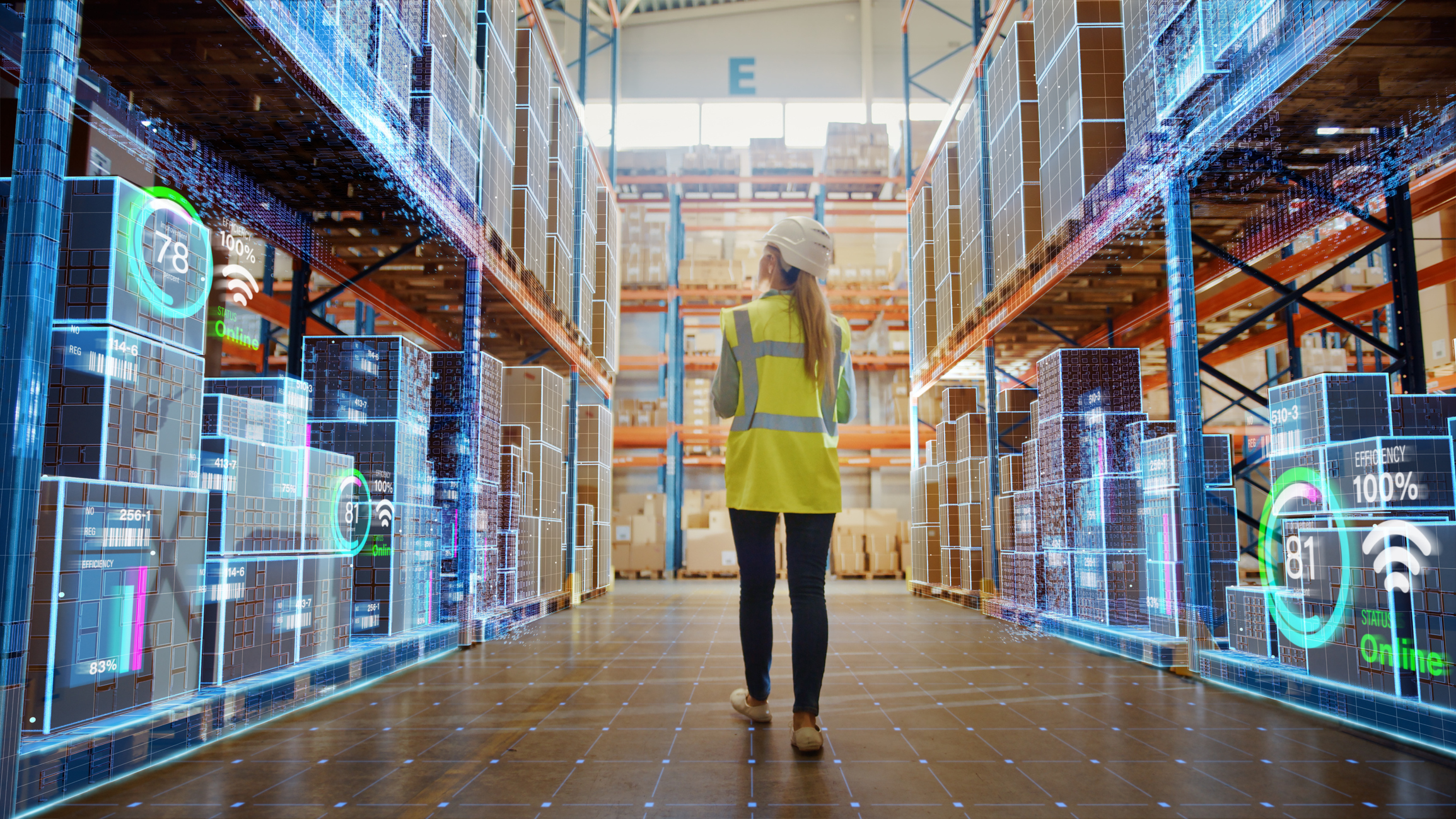
5 Ways to Improve Dispatch Efficiency in Your Warehouse
Efficient dispatch operations are crucial for any warehouse looking to meet customer demands, reduce errors, and optimise costs. In today’s fast-paced logistics environment, a well-structured dispatch process ensures orders are shipped accurately and on time, keeping customers satisfied and operations running smoothly.
Continue reading...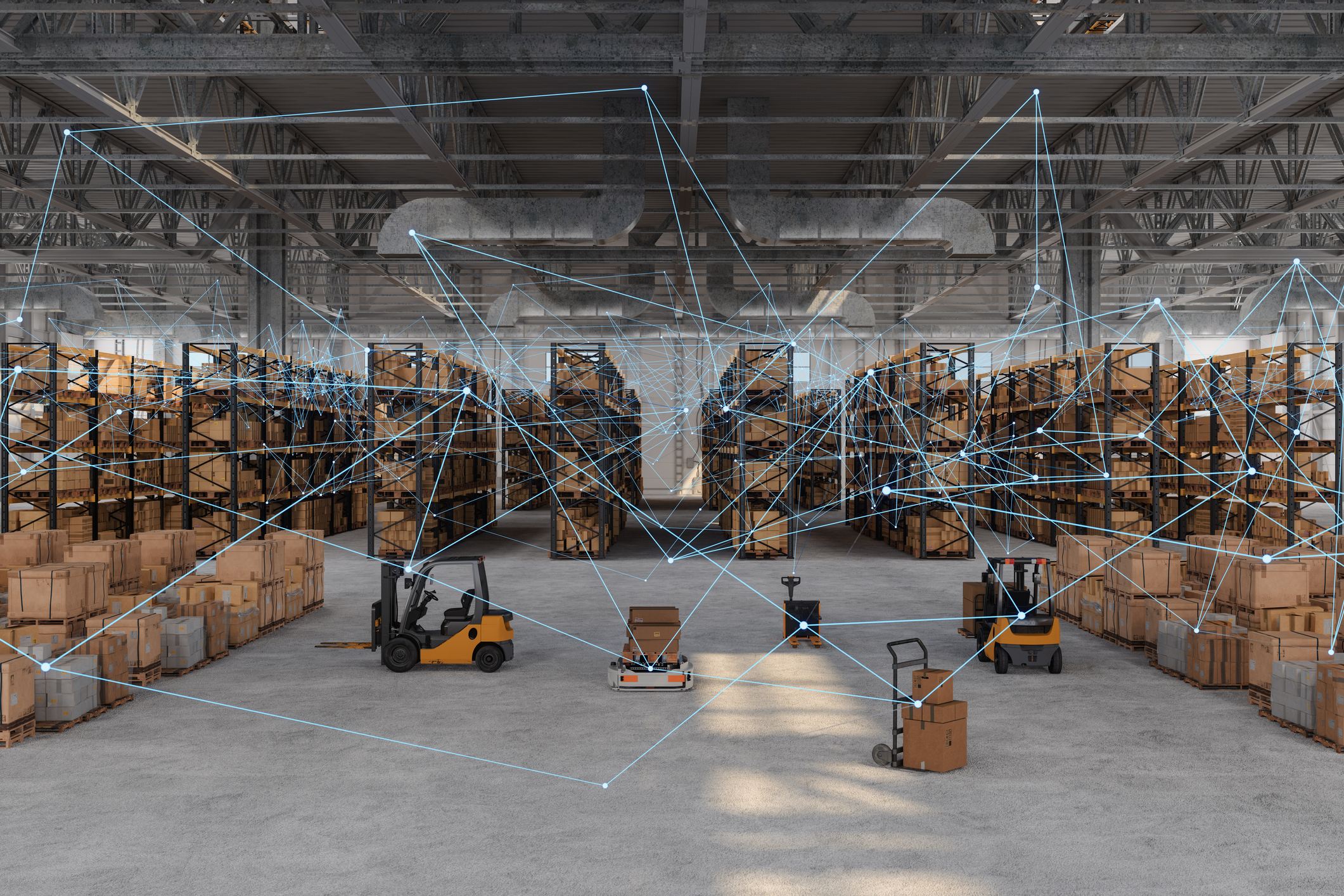
Top 5 Benefits of a WMS for your 3PL Business:
Discover how a 3PL WMS can transform your business operations and drive growth from the expert team at Optima.
Continue reading...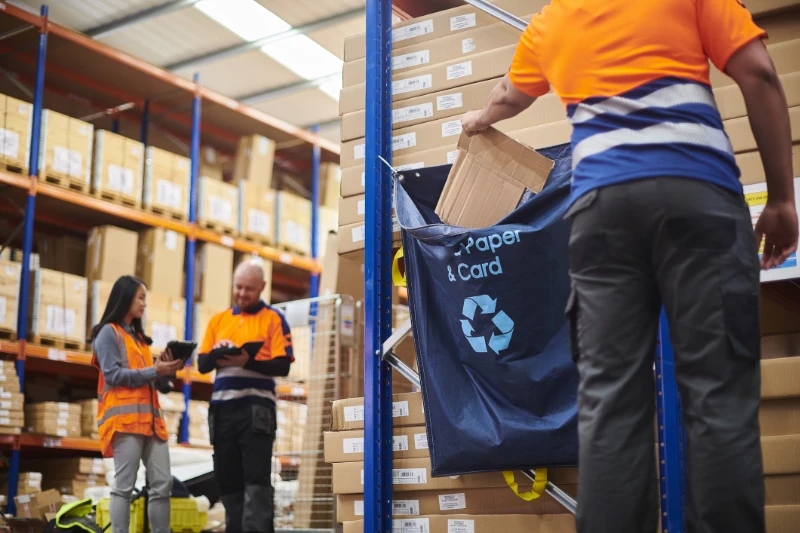
How to reduce waste in your warehouse
If you are considering optimising your warehouse operations to promote sustainability and reduce waste, at Optima WMS we can help.
Continue reading...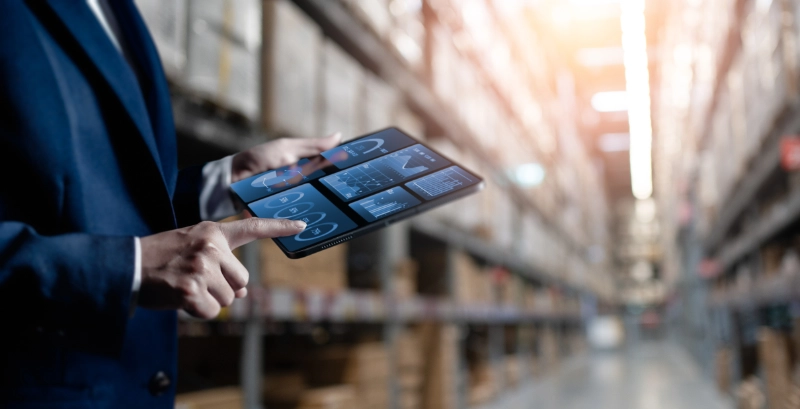
The 5 Inventory Cost Categories
Inventory represents the financial lifeblood of many businesses; simply put, if there is no stock to be sold, there is no business. So it’s crucial to understand inventory and all the costs that are associated with it. Inventory cost types can be broken down into five key categories: Ordering, Holding, Spoilage, Inventory shrinkage and Stockout costs. This article looks at the various types of inventory costs you can expect to find within each category.
Continue reading...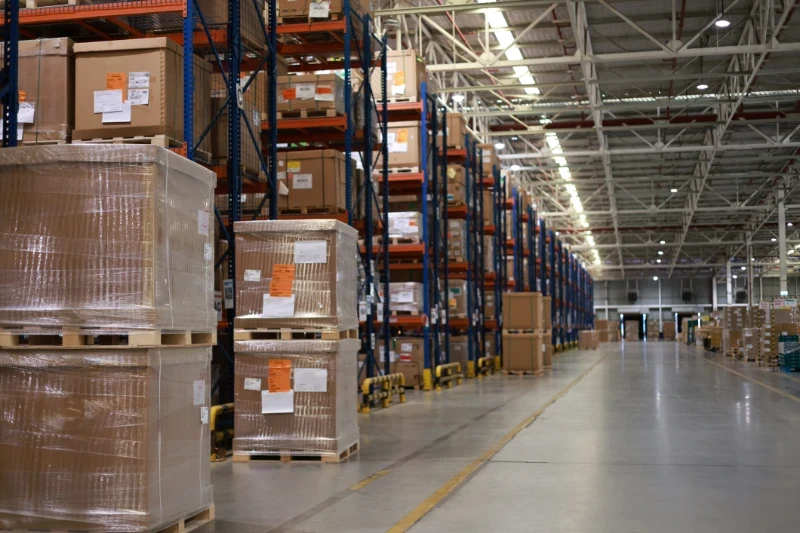
What is 3PL?
In supply chain management, efficiency and optimisation are paramount, and one key strategy that has emerged to meet these demands is third-party logistics, commonly known as 3PL. 3PL companies provide valuable services to businesses that primarily don’t focus on logistics themselves, freeing them up to concentrate on their main business operations.
Continue reading...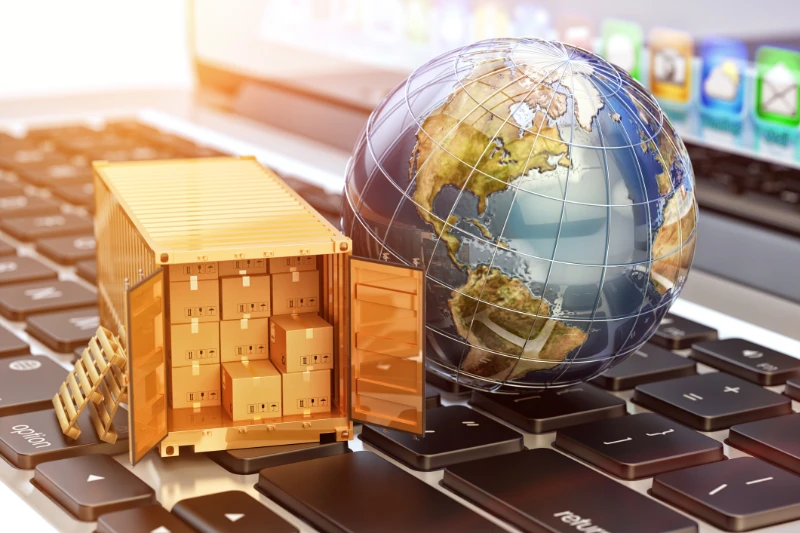
Guide to international warehousing
Are you a logistic professional, supply chain manager, or business involved in international trade and looking to understand the various options and considerations for your warehousing needs? If so, this guide has everything you need to know about international warehousing. For businesses looking to expand their reach, reduce delivery times, and improve customer satisfaction, international warehousing is a safe and affordable way of storing and distributing goods abroad. International warehouses allow businesses to import, store, and ship to audiences in countries abroad and expand their global reach while ensuring timely deliveries, reduced transportation costs, and improved customer experience.
Continue reading...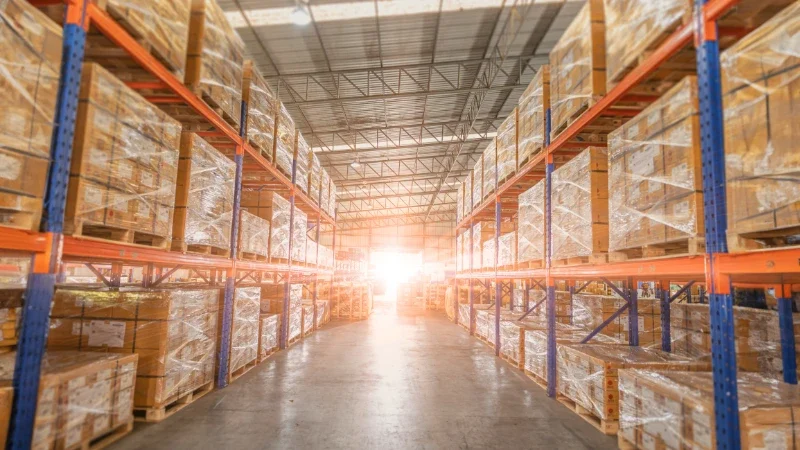
What Makes a Good Warehouse?
Having an efficient and well-organised warehouse is one of the most critical factors in operating a successful supply chain. The logistics behind warehouse operations can be complex and often require expert warehouse management systems to ensure their ongoing success. There are a number of key areas that come into play when deciding what makes a good warehouse – each area must run harmoniously alongside the other. A lapse in any area may result in the cycle of the business suffering. This can ultimately lead to delays in fulfilment and poor customer service. We’ve broken down some of the most important elements that make a successful and efficient warehouse.
Continue reading...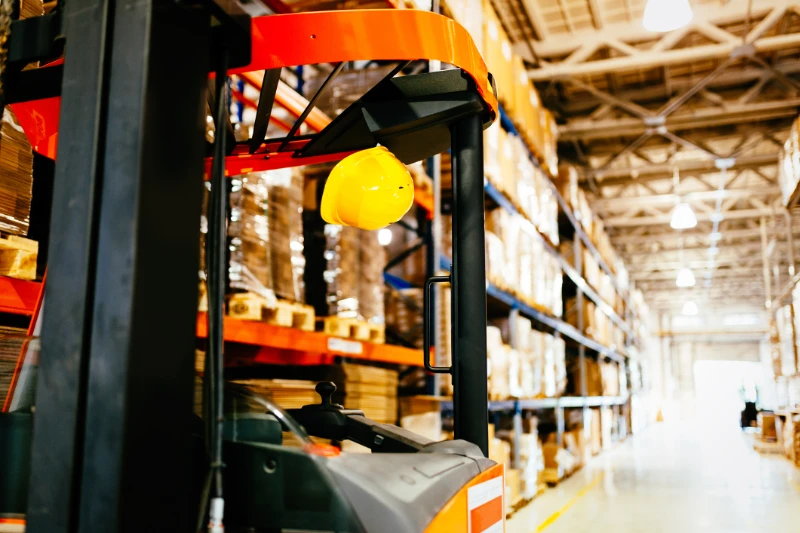
Warehouse Quality Control.
At its core, quality control involves the implementation of processes and procedures to ensure that products meet predetermined standards of quality before they are shipped to customers. These QC methods include inspection, testing and documentation to identify and rectify any defects or deviations from quality standards.
Continue reading...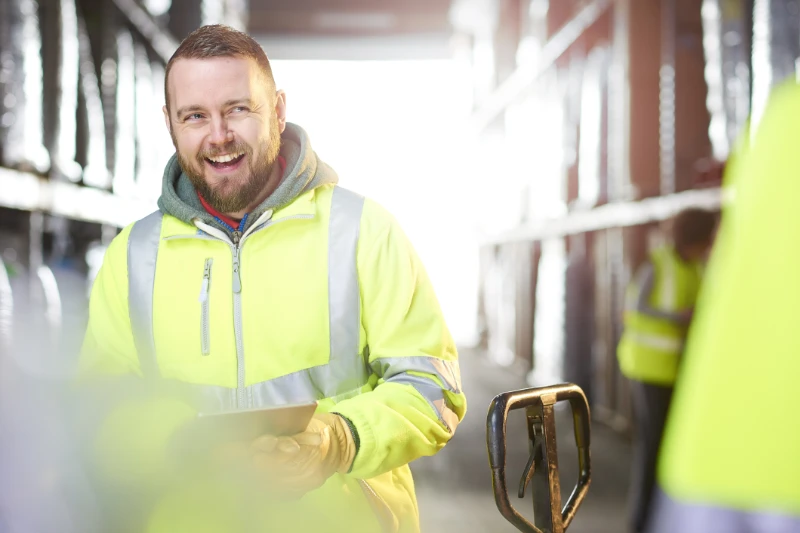
How to boost staff morale in a warehouse
Warehouse work can be physically demanding and mentally challenging, so it’s no surprise that morale amongst staff can sometimes drop. which can have a big impact on their productivity, focus and accuracy, not to mention their length of service and, ultimately, your bottom line.
Continue reading...Ready to take control of your warehouse?
Contact us today to chat with our friendly team and explore a demo showcasing how Optima can transform your business.